Drukarki 3D znajdujące się w obszarze produkcji aparatów słuchowych stanowią wizytówkę nowoczesnej i zaawansowanej technologicznie produkcji realizowanej w firmie DGS Poland Sp. z o.o. Drukarki 3D stanowią bowiem rdzeń produkcji aparatów słuchowych ITE, umożliwiając realizację kilkuset zleceń dziennie. Za ich pomocą wykonywane są obudowy aparatów w różnych wariantach kolorystycznych – w oparciu o różne żywice światłoutrwaldzalne (fotopolimerowe). Większość z nas rozpoczyna i kończy swój dzień pracy w bliskim kontakcie z procesem druku 3D w technologii DLP.
Czym jest zatem technologia drukowania 3D DLP i jak to działa? Postaram się przybliżyć poniżej.
Technologia druku 3D DLP (Digital Light Processing) jest systemem wytwarzania przyrostowego polegającym na utwardzaniu ciekłego materiału (żywicy fotopolimerowej) za pomocą światła. W tym procesie źródłem światła jest natomiast specjalny projektor DLP. Budowanie trójwymiarowego obiektu (w naszym przypadku obudowy aparatu słuchowego) następuje poprzez układanie kolejnych warstw materiału – jedna po drugiej).
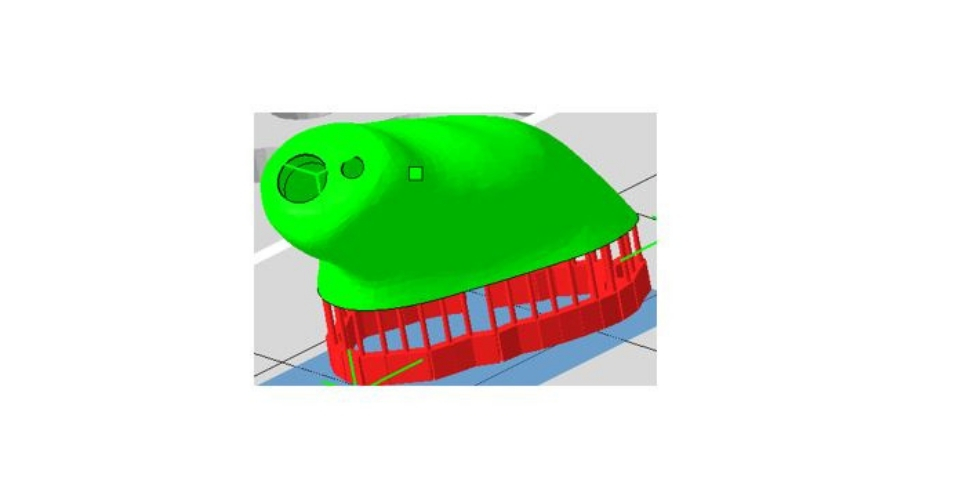
Powyższe zdjęcie ilustruje wymodelowaną obudowę aparatu słuchowego (kolor zielony).
Kolor czerwony natomiast to "supporty" – czyli inaczej mówiąc wsporniki, dodawane systemowo dla każdego drukowanego obiektu – celem łatwiejszego i szybszego odseparowania drukowanego elementu po zakończonym procesie drukowania 3D - od powierzchni na której element ten jest drukowany (platforma budująca).
Proces drukowania obiektu trójwymiarowego
Oprogramowanie dedykowane dla drukarek 3D dzieli obiekt trójwymiarowy (zapisany w postaci pliku graficznego na poprzednich etapach procesu produkcji – skanowanie, modelowanie) na poszczególne warstwy, dokładnie co 100 mikronów. Każda warstwa więc to nie inaczej jak wygenerowany obraz 2D, który wyświetlany jest przez projektor drukarki 3D – jeden po drugim.
.jpg?la=pl-pl&rev=ED13&hash=ED676E03C8C6EF03143706F4F1C2F5DC)
Dla lepszego zrozumienia procesu drukowania 3D w technologii DLP można posłużyć się poniższym obiektem trójwymiarowym – na przykładzie kuli.
.jpg?la=pl-pl&rev=A147&hash=0A2CA98A1160B5404A9DD4ADD11DB94D)
Wysokość obiektu trójwymiarowego to 40 milimetrów, a więc 4 cm. Jak zostało wspomniane powyżej, oprogramowanie drukarki 3D dzieli obiekt trójwymiarowy kuli – na poszczególne warstwy, dokładnie co 100 mikronów (100 mikronów = 0,1 milimetra).
A więc jeśli obiekt trójwymiarowy ma wysokość 4 cm (40 milimetrów), to system dzieląc obiekt na warstwy co 100 mikronów każda, wygeneruje 400 warstw (obrazów 2D).
Następnie każda z tych warstw wysyłana zostaje do systemu drukarki i wyświetlana przez projektor – kolejno po sobie.
.jpg?la=pl-pl&rev=55C7&hash=606A215C5805E0F0F54BDF05967C9C4A)
Rozpoczynając proces drukowania 3D, projektor znajdujący się we wnętrzu drukarki 3D wyświetla obraz (każdą warstwę) jedna po drugiej, przy zachowaniu określonej (zaprogramowanej) sekwencji czasowej, aż do momentu wyświetlenia ostatniej warstwy – zakończenie procesu drukowania 3D.
.jpg?la=pl-pl&rev=A5C3&hash=5F6CD577632322CFDF19782EFF8995EC)
.jpg?la=pl-pl&rev=EF64&hash=11F4112EA287A224EDFBB07A837BEFC3)
.jpg?la=pl-pl&rev=40B1&hash=E8A66F1EBF3D9EABDB2A914C9B08ADAB)
.jpg?la=pl-pl&rev=20C9&hash=60902A9203540F076623A4B6F71F24F1)
Bardzo ważnym faktem i niewątpliwie wpływającym na możliwości produkcyjne jest to, że proces drukowania nie ogranicza się tylko i wyłącznie do jednego wybranego obiektu trójwymiarowego.
O ilości obiektów drukowanych podczas jednego wydruku, decyduje ich wielkość oraz powierzchnia platformy budującej oraz wyświetlanego przez projektor obrazu. Czas realizacji wydruku natomiast determinowany jest nie przez liczbę obiektów a przez ich wysokość – najwyższy obiekt trójwymiarowy (ilość warstw). Więc dla lepszego zobrazowania – zakładając, że mamy 15 identycznych obiektów o wysokości 20 milimetrów i jeden obiekt o wysokości 40 milimetrów – czas wydruku determinuje tylko ten jeden - najwyższy obiekt (wszystkie obiekty 20 milimetrowe są już wydrukowane, jednak obiekt 40 milimetrowy jest wciąż drukowany – pozostało 200 kolejnych warstw).
.jpg?la=pl-pl&rev=10B9&hash=696C36416A55C5D89A9AE330FEBB024C)