Zdalna kalibracja maszyny w Stanach czy przeniesienie produkcji w Chinach to jedne z największych wyzwań nowej rzeczywistości, z którymi z powodzeniem zmierzyli się członkowie Globalnego Działu Technologii i Inżynierii w Demant. Przemysław, szef działu, opowiedział nam o ich codziennej pracy, o wyzwaniach, z jakimi musieli się mierzyć w związku z pandemią koronawirusa Covid-19 i o tym, jak dbać o wzajemne relacje w rozproszonym zespole.
Anna: Na czym polega praca w Globalnym Dziale Technologii i Inżynierii?
Przemysław: Zajmujemy się wszystkim, co jest związane z produkcją aparatów wewnątrzusznych. Nasz udział widoczny jest już na etapie designu, gdzie współpracujemy z Działem R&D i jesteśmy obecni podczas ścieżki projektowania urządzenia. Dzięki sporej sieci kontaktów w Grupie Demant możemy dzielić się wiedzą i pomysłami również z innych oddziałów, a także odpowiadać na istniejące potrzeby proponując usprawnienia już na początkowym etapie prac. Pomysły i rozwiązanie przekładamy na język techniczny, aby możliwe było sprawdzenie ich skuteczności. Następnie razem z Działem Service & Custom NPI z Danii współpracujemy nad wdrożeniem produktu – zaczynając od testów na prototypach, a kończąc na pre-production assembly, czyli finalnym teście przed jego wypuszczeniem.
Czym jeszcze zajmujecie się w swojej pracy?
Nasi specjaliści czuwają nad prawidłową konfiguracją produktu, aby funkcje wybrane przez użytkownika końcowego i jego protetyka słuchu były możliwe do realizacji w procesie produkcyjnym - od wzmocnienia aparatu dopasowując go do stopnia ubytku słuchu po bluetooth. Wybraną konfigurację przekładamy na język zlecenia produkcyjnego.
Nasza współpraca ze wspomnianym Działem Service & Custom NPI polega również na przygotowywaniu dokumentacji związanej z wypuszczeniem nowego produktu. Następnie my zajmujemy się jej utrzymaniem i aktualizacją. Dodatkowo prowadzimy wewnętrzny portal dokumentacyjny, do którego dostęp mają między innymi wszystkie jednostki produkcyjne.
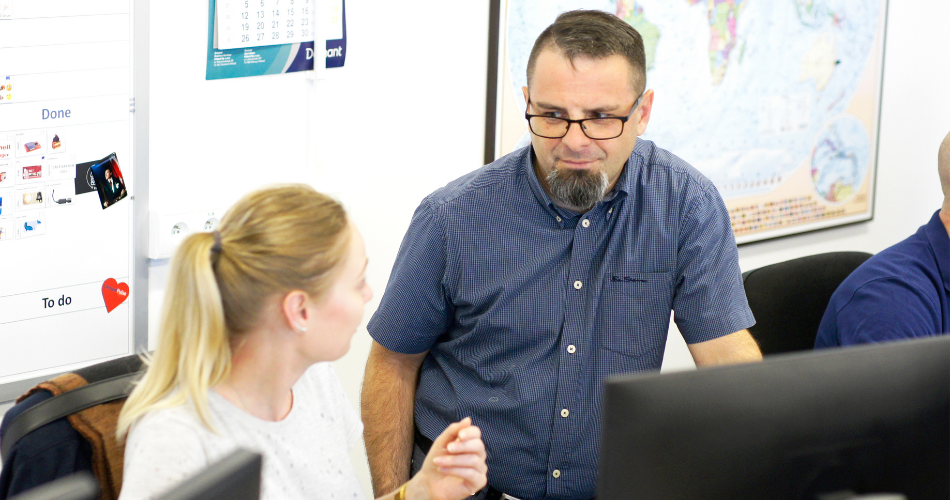
Jak dbacie o zapewnienie utrzymania produkcji aparatów wewnątrzusznych i serwisu w Grupie Demant?
W naszym zespole jest Dział Wsparcia, który składa się z inżynierów pracujących w każdym dużym oddziale produkcyjnym na świecie. W Polsce są to 4 osoby i po jednej w Australii, Chinach, Stanach i Meksyku. Osoby te są strażnikami standardu produkcji i serwisu naszych aparatów, a także dbają o utrzymanie maszyn i wspierają najbliższe sobie mniejsze jednostki produkcyjne, które nie mają lokalnego wsparcia inżynieryjnego. Mamy również kierowników projektów, którzy dbają o inicjatywy z naszego portfolio projektowego – ich realizację i wdrożenie.
Co oznacza słowo „globalny” w nazwie działu?
W Grupie Demant mamy 16 jednostek produkcyjnych. Wyobraźmy sobie sytuację, że każda z nich robi wszystko według swoich standardów. Wówczas podczas audytu MDSAP, gdzie dla kilku jednostek w różnych miejscach mamy jeden certyfikat, każdy odział miałby swoją strukturę dokumentacji, potrzebowałby indywidualnych zatwierdzeń finalnych produktów, nie wspominając o projektowaniu samych procesów. Z perspektywy firmy łatwiej jest mieć to scentralizowane niż posiadać w każdej jednostce dział inżynierii, który będzie działał na rynku lokalnym.
Inżynieria lokalna oczywiście jest bardzo ważna dla utrzymania czynności operacyjnych i rozwiązywania codziennych problemów. Mamy grupy inżynieryjne podzielone na rejony, w których wymieniają się pomysłami i dokonanymi usprawnieniami procesów. Dzięki temu możemy przygotować globalne rozwiązania działające lokalnie – musimy przy tym pamiętać, żeby były dopasowane do małych i dużych jednostek.
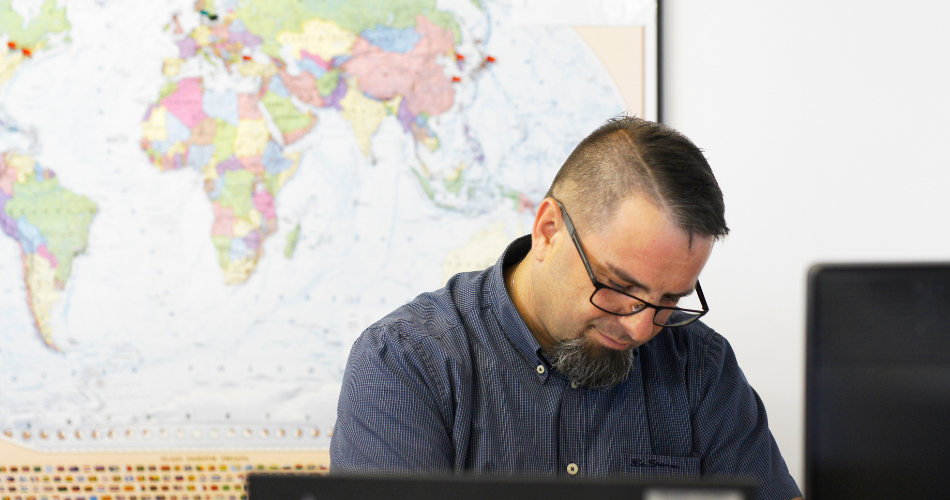
Wasza praca wiąże się z częstymi wyjazdami, również w odległe zakątki świata. Jak to wyglądało w ciągu ostatniego roku?
Było to spore wyzwanie. Przynajmniej raz w roku byliśmy w każdej jednostce produkcyjnej, żeby przeprowadzić roczny przegląd maszyn i sprawdzić, czy wszystkie procedury są przestrzegane. Musieliśmy zmienić podejście i wymyśleć rozwiązanie dopasowane do nowych realiów. W czasie pandemii koronawirusa Covid-19 mocno rozwinęły się technologie i możliwości, dzięki czemu mogliśmy dokonać zdalnej kalibracji drukarki 3D w Stanach, co pozwoliło na kontynuację produkcji bez kosztownej i niebezpiecznej dla sprzętu wysyłki. Powstały również fora dyskusyjne, gdzie możemy wymieniać się wiedzą czy rozwiązaniami.
Jakie było Wasze największe wyzwanie?
Udało nam się zdalnie przenieść produkcję do nowej lokalizacji w Szanghaju. W związku z pandemią nie mogliśmy być na miejscu, więc wszystkie spotkania odbywały się on-line. Przeniesienie produkcji to bardzo duże zadanie, który składa się między innymi z zaprojektowania wnętrza, przeprojektowania obecnie dostępnych przepływów, tak, aby były zgodnie z planem rozwoju na najbliższe lata. Nasz lokalny inżynier zajmował się montowaniem maszyn, a my wspieraliśmy go w przygotowaniu do lokalnej certyfikacji, przy przeprowadzaniu walidacji i odpowiednim udokumentowaniu wszystkich niezbędnych aktywności. Dodatkowo samo przeniesienie musiało wydarzyć się w ciągu weekendu – nie mogliśmy przerwać ciągłości procesów produkcyjnych.
Nieco mniejszym projektem było wsparcie zmiany systemu ERP w jednostce w Hiszpanii i przeprowadzka w nowy obszar. Kilka spotkań online przy wsparciu specjalisty Lean z Polski oraz virtual tour po nowym obszarze pozwolił nam przetestować i sprawdzić poprawność zaimplementowanego procesu. Ograniczenia jakie mieliśmy i dostępne rozwiązania technologiczne pokazały, że nie ma rzeczy niemożliwych.
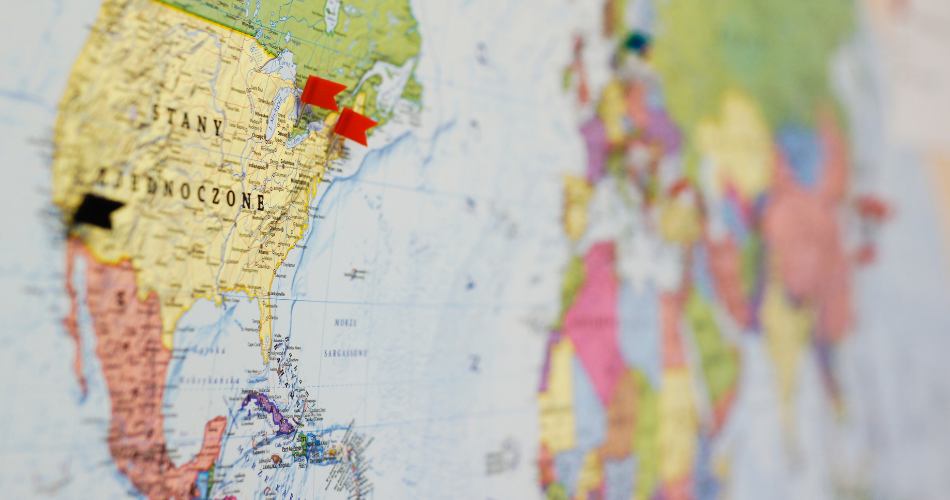
Global Training Organization – czym jest i dlaczego powstało?
Bardzo ważną funkcje w zespole pełnią trenerzy, którzy zajmują się przygotowaniem materiałów szkoleniowych i przeszkoleniem pracowników z tego, w jaki sposób produkować i serwisować nasze aparaty, we wszystkich jednostkach produkcyjnych w Grupie Demant. Aby zaspokoić rosnące potrzeby szkoleniowe powstała wewnętrzna inicjatywa Global Training Organization, zrzeszająca trenerów z całego świata – na dziś jest to ponad 40 osób. Dzięki temu jesteśmy w stanie szybko reagować na zapytania treningowe, w mniejszym stopniu odczuwamy brak możliwości przemieszczania się i jesteśmy w stanie dzielić się wiedzą i umiejętnościami w grupie trenerów.
W naszym zespole jest global training coordinator, do którego trafiają zapotrzebowania na szkolenia, i który zajmuje się doborem trenera z odpowiednimi kompetencjami, pomaga w przygotowaniu sesji treningowej, pakietu materiałów i w miarę potrzeb wspiera sam trening. Osoba ta dba również o kontakty z firmami exportowymi.
Zajmujcie się wdrażaniem nowatorskich rozwiązań z użyciem najnowszych technologii? Na czym to polega?
Szukamy najlepszych możliwych rozwiązań, które pozwolą nam usprawnić i zoptymalizować procesy produkcyjne. Takim przykładem może być urządzenie do wycinania faceplatów. Wcześniej robiono to ręcznie, teraz model wkładamy do maszyny i wyjmujemy gotowy kształt. Obecnie pracujemy nad wdrożeniem tego rozwiązania w naszych fabrykach w Meksyku, Chinach i Australii. Innowacyjność to również „kwestionowanie tego co robimy”. Staramy się wyjść poza utarte schematy i znaleźć nowe możliwości, które nie tylko usprawniają procesy, ale pozwalają je skrócić. Out of the box to podejście, które pozwala stworzyć rozwiązania jakich jeszcze nikt nie próbował lub nie wie, że są możliwe.
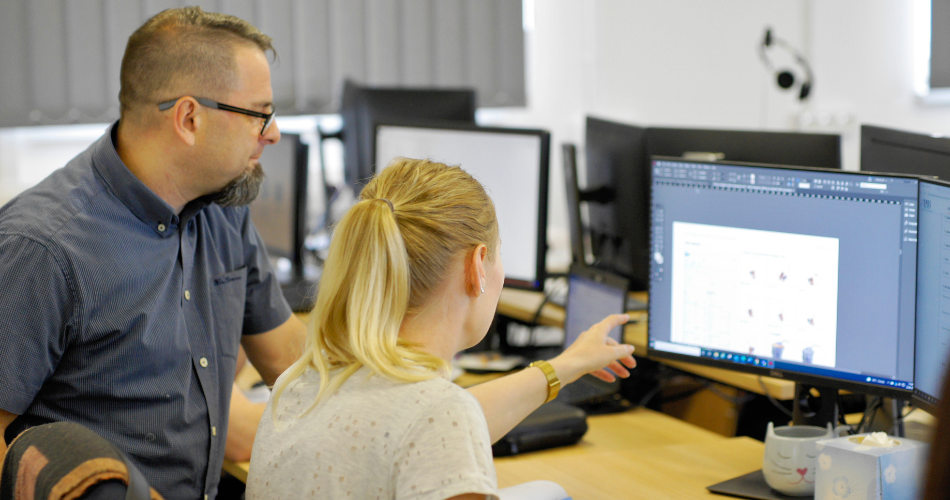
Praca w Globalnym Dziale Inżynierii i Technologii to również możliwość uczestnictwa w szkoleniach i konferencjach branżowych?
Co roku firma RapidShape, która dostarcza nam rozwiązania w drukowaniu 3D, zaprasza naszych inżynierów z Grupy Demant na zaawansowane szkolenie do swojej siedziby pod Stuttgartem. Omawiana jest tam budowa oraz serwis urządzeń i nowe rozwiązania w dziedzinie druku 3D, a samo szkolenie jest dopasowane do naszych potrzeb technologicznych.
Byliśmy też zaproszeni jako prelegenci na konferencji AMM 2019 event we Wrocławiu, gdzie prezentowaliśmy rozwiązania w produkcji aparatów wewnątrzusznych z wykorzystaniem urządzeń w druku 3D.
Monika z naszego zespołu uczestniczyła w szkoleniu w Algierii, gdzie pokazywała jak prawidłowo pobrać wycisk, a Piotr, w ramach akcji Fundacji Williama Demanta w Kenii, pomagał w jednej z lokalnych klinik zainstalować sprzęt do dopasowania aparatu oraz uczył jak aktualizować oprogramowanie i jak wykonać podstawowy serwis urządzenia.
Wasza praca to częste wyjazdy, jakie ciekawe miejsca udało wam się zobaczyć dzięki pracy?
Piotr jest jedyną osobą z zespołu, która była we wszystkich jednostkach produkcyjnych. Najchętniej wspiera oddział w Brazylii i te pobyty wspomina najmilej. Na mnie największe wrażenie zrobiła Australia, ale generalnie uwielbiam wyjazdy i eksplorowanie nowych miejsc i kultur. Przy okazji takich podróży służbowych wiele razy doświadczyłem tego, że moje imię i nazwisko jest przyczynkiem do śmiesznych sytuacji lub sposobnością do znacznego skrócenia dystansu w relacjach przy pierwszym poznaniu.
Jak dbacie o ducha zespołu na co dzień będąc w tylu miejscach na świecie?
Najważniejsze to utrzymanie kontaktu. Niestety sytuacja pandemiczna chwilowo uniemożliwiła nam spotkania bezpośrednie z osobami pracującymi w innych lokalizacjach. Do marca 2020 roku regularnie widzieliśmy się dwa razy w roku. Wykorzystywaliśmy również każdą dodatkową okazję poprzez zorganizowanie swojej pracy tak, aby w przypadku wizyty w jednej jednostce produkcyjnej móc się spotkać z osobami będącymi w bliskiej odległości.
Mamy niepisaną zasadę, że przy spotkaniach online zawsze mamy włączone kamery. Na miejscu dwa razy w tygodniu widzimy się całym zespołem. Na początku tygodnia omawiamy zadania, a pod koniec sprawdzamy ich statusy. Raz w miesiącu mamy globalne spotkanie on-line z tymi, którzy na co dzień pracują od Meksyku po Australię.
Moją osobistą dewizą jest to, aby nigdy nie zostawiać kogoś z problemem samemu sobie. W naszej pracy codziennie budujemy mosty - czy to wewnątrz zespołu czy pomiędzy ludźmi z odległych zakątków świata. Wspólnie szukamy rozwiązań i możliwości jak sprawić, żeby osobom z ubytkiem słuchu żyło się lepiej.
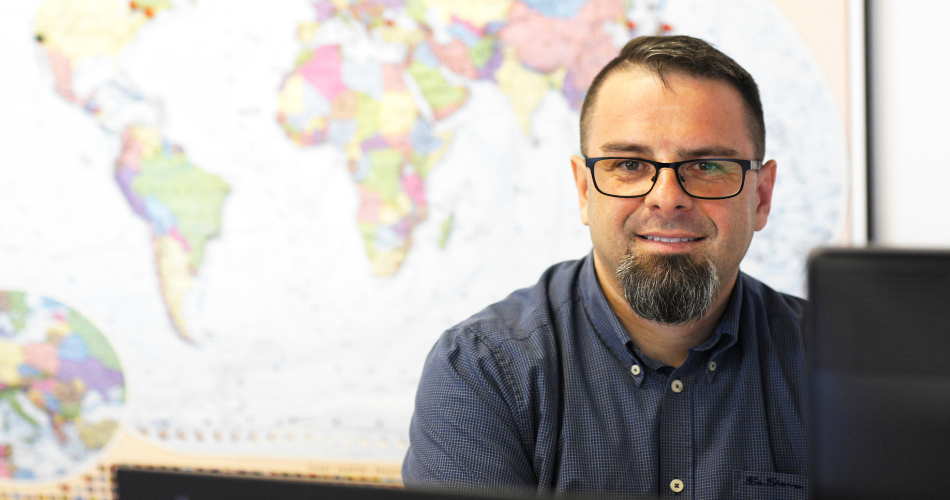